Failure
Creep can occur in metals and other materials subjected to a constant load, normally much lower than the yield stress, for a long time. Gradual deformation takes place due to a number of mechanisms, including:
- the movement of dislocations
- grain boundaries sliding relative to each other
- necking.
Lead pipes and roofing gradually become deformed under their own weight due to the effects of creep.
Creep affects structures such as the steel cables used to support suspension bridges, but it is more significant in metals used at temperatures that are above 0.3 × the melting point of the metal in K. This is the case for lead used at room temperatures and also for metals used in engines.
Creep-resistant alloys have been developed for use in applications where failure due to creep could be disastrous, for example, in the turbine blades used in aircraft jet engines.
Fatigue is another type of failure caused by a cumulative effect over time. It affects metals subjected to repeated cycles of stress such as that caused by stretching, rotation or vibration. Fatigue failure starts with a small crack appearing due to repeated working. Once a crack has formed, stress builds up around it due to the reduction in cross-sectional area. This causes the crack to enlarge until the material fractures.
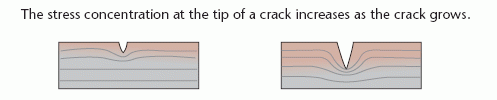
The risks of fatigue failure can be reduced during both design and manufacture. In designing structures that are subjected to repetitive stress, sharp corners should be avoided as this is where cracks can develop. In the manufacturing process, care should be taken to avoid poor workmanship at places where materials are rivetted or bolted together leaving tiny cracks that then propagate.