Steel
The behaviour of steel under stress depends on the carbon content of the metal. High carbon steels such as cast iron are brittle; they snap just beyond the elastic limit. Mild steel is tougher, much more energy is needed to cause failure. The diagram below compares stress–strain graphs for high carbon steel and mild steel.
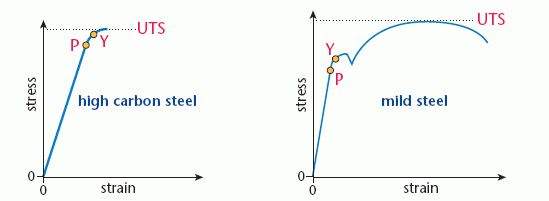
Mild steel can be deformed plastically, so it is used in place of wrought iron to make structures such as iron gates.
The points marked on the graphs are:
- P, the limit of proportionality; this is the end of the Hooke’s law region
- Y, the elastic limit or yield point; beyond this point the material is permanently deformed
- UTS, the ultimate tensile stress or breaking stress; the maximum stress that the material can withstand.
Metals have a polycrystalline structure, which means that they consist of many small crystals. Within each crystal the atoms are arranged in a regular pattern. This structure is shown in diagram (a), which also shows the slip planes within the crystals. The ductile behaviour of mild steel beyond its elastic limit is due to whole planes of atoms slipping against each other. Slip occurs readily by the movement of an edge dislocation; a defect in the crystal due to an incomplete plane of
atoms. This is shown in diagram (b).
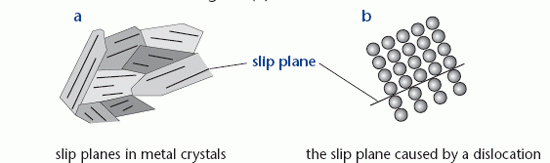
The term ‘poly’ means ‘many’ and ‘crystalline’ refers to atoms ‘arranged in a regular array’ to form crystals. The crystalline nature of metals can be seen clearly on the zinc coating on the inside of a can of pineapple.
When slip occurs in a metal it can result in necking. If the width of the sample decreases at one point, the stress increases due to the reduction in cross-sectional area. The increased stress causes further stretching and narrowing at this point until the metal eventually fractures.
The ‘neck’ refers to the narrowing of the sample; this is sometimes called a ‘waist’.
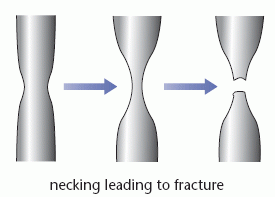