Stock Control
This section explains Stock Control covering, Interpretation of Stock Control Diagram, Buffer Stocks, Implications of Poor Stock Control, Just in Time (JIT) Management of Stock, Waste Minimisation and Competitive Advantage from Lean Production.
Effective stock control is vital for businesses to ensure that they maintain the correct level of inventory, reduce costs, and meet customer demand without unnecessary wastage or stockouts. Understanding stock control systems, such as Just in Time (JIT) and lean production techniques, can give businesses a competitive advantage by improving operational efficiency.
Interpretation of Stock Control Diagram
A stock control diagram (also known as a re-order level chart) is a visual representation of how stock levels fluctuate over time. It helps businesses monitor and manage inventory levels to ensure that they do not run out of stock or hold excessive inventory.
Key Elements of a Stock Control Diagram:
- Re-order Level: This is the point at which a business needs to order more stock. It is usually calculated based on the lead time (the time between ordering and receiving goods) and the average demand for the product during that period.
- Re-order Quantity: This refers to the amount of stock that should be ordered each time stock levels reach the re-order point. It is typically determined based on the economic order quantity (EOQ), which seeks to balance ordering costs with holding costs.
- Lead Time: The time taken from ordering the stock to its arrival.
- Maximum Stock Level: The upper limit of stock that a business can hold, beyond which additional stock would be wasteful or too costly to store.
- Minimum Stock Level (Buffer Stock): The lowest level of stock that should be maintained to ensure there is enough inventory during the lead time before new stock arrives.
Diagram Example:
A typical stock control diagram will show a declining line representing stock levels, with the re-order level marked as a point where stock should be replenished. Between the maximum and minimum stock levels, businesses aim to maintain stock levels to meet demand without overstocking.
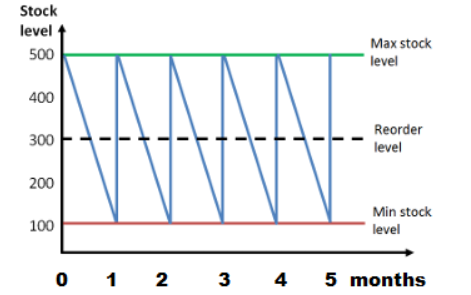
Buffer Stocks
Buffer stock, also known as safety stock, is the minimum amount of stock a business keeps to prevent stockouts during unexpected fluctuations in demand or delays in delivery.
Purpose of Buffer Stock:
- Avoid Stockouts: Buffer stocks act as a cushion against unexpected increases in demand or delays in supply, ensuring that production or sales are not disrupted.
- Smooth Operations: They provide a safety net in case of unforeseen circumstances, such as suppliers failing to deliver on time or sudden spikes in customer demand.
However, it is important to strike a balance: maintaining too much buffer stock can tie up capital in inventory and increase storage costs, while too little can lead to stockouts, lost sales, and customer dissatisfaction.
Determining Buffer Stock:
The level of buffer stock depends on:
- Lead Time: The longer the lead time, the higher the buffer stock needed.
- Demand Variability: If demand is unpredictable, a higher buffer stock may be necessary.
- Cost of Stockouts: If the cost of running out of stock is high (e.g., losing a sale), a business may opt to keep a higher buffer stock.
Implications of Poor Stock Control
Poor stock control can lead to significant operational challenges and financial losses. The main implications include:
- Stockouts: Running out of stock (stockouts) can result in lost sales, reduced customer satisfaction, and damage to the business’s reputation. If a business frequently experiences stockouts, customers may turn to competitors.
- Excess Stock: Holding too much stock ties up capital in inventory that could be used for other purposes, such as investment or paying off debts. Excess stock also incurs storage costs and may become obsolete or deteriorate over time (especially in the case of perishable goods).
- Increased Costs: Poor stock control can lead to higher costs in several areas:
- Holding Costs: Storing excess stock increases warehousing and insurance costs.
- Ordering Costs: Frequent ordering due to inaccurate stock levels can increase administrative and transportation costs.
- Loss of Discounts: Failure to order in optimal quantities can prevent a business from benefiting from bulk purchasing discounts.
- Inefficiencies in Production: If stock is not available when needed for production, manufacturing operations may be delayed or interrupted, resulting in inefficiency and missed deadlines.
- Negative Cash Flow: Overstocking means a business spends more money purchasing stock than it needs, leading to poor cash flow management. Conversely, understocking may lead to lost opportunities to make sales.
Just in Time (JIT) Management of Stock
Just in Time (JIT) is a stock control system designed to minimise inventory levels by ordering and receiving stock only when it is needed for production or to fulfil customer orders. The goal is to reduce holding costs and eliminate waste, enabling businesses to operate more efficiently.
Key Features of JIT:
- Reduction of Inventory Levels: JIT aims to keep stock levels as low as possible, reducing the need for warehousing and storage.
- Frequent Orders: Stock is ordered in small quantities, often just in time for use in production or to meet customer demand.
- Reliance on Suppliers: JIT requires suppliers to deliver goods quickly and reliably, often on a daily or weekly basis.
Benefits of JIT:
- Lower Inventory Costs: By reducing the amount of stock held, businesses can lower warehousing costs and reduce the risk of stock becoming obsolete or damaged.
- Increased Efficiency: JIT encourages streamlined production processes and eliminates waste by ensuring that materials are used as soon as they arrive.
- Improved Cash Flow: With less money tied up in stock, businesses can improve cash flow and reinvest savings into other areas of the business.
Challenges of JIT:
- Dependence on Suppliers: JIT relies heavily on suppliers' ability to deliver on time and meet quality standards. Any disruption in the supply chain can lead to production delays.
- Vulnerability to Demand Fluctuations: JIT works well when demand is stable, but it can lead to problems if demand spikes unexpectedly, as there may not be sufficient stock to meet customer needs.
Waste Minimisation
Waste minimisation refers to the process of reducing waste at every stage of production or service delivery. This can include material waste, time waste, or even waste in human resources. The aim is to reduce unnecessary consumption of resources, lower costs, and contribute to sustainability efforts.
Techniques for Waste Minimisation:
- Lean Production: This method involves identifying and eliminating non-value-added activities in the production process, such as excess motion, waiting times, and unnecessary transportation.
- Quality Control: Ensuring that products are manufactured to the required specifications reduces the need for rework or wastage.
- Better Forecasting: Accurate demand forecasting helps reduce the likelihood of overproduction, which can lead to waste.
- Efficient Resource Use: Optimising the use of materials, energy, and labour can help businesses reduce waste and improve productivity.
Benefits of Waste Minimisation:
- Cost Savings: Reducing waste directly lowers operational costs, leading to higher profitability.
- Environmental Impact: Waste minimisation is often aligned with sustainability goals, helping businesses reduce their environmental footprint.
- Improved Efficiency: Streamlined operations and fewer disruptions lead to increased efficiency across the supply chain.
Competitive Advantage from Lean Production
Lean production is a management philosophy that focuses on minimising waste, maximising efficiency, and continually improving production processes. By adopting lean principles, businesses can gain a competitive advantage in several ways:
- Cost Reduction: Lean production helps businesses reduce waste in materials, time, and labour, leading to significant cost savings. Lower production costs allow businesses to offer more competitive pricing, increasing their appeal to customers.
- Improved Product Quality: Lean production emphasises continuous improvement (known as Kaizen) and quality control at every stage of production. This leads to higher-quality products, fewer defects, and greater customer satisfaction.
- Faster Response to Customer Demand: By eliminating inefficiencies and reducing stock levels (as in JIT), businesses can respond more quickly to changes in customer demand. This flexibility can be a significant advantage in dynamic and competitive markets.
- Enhanced Customer Value: By focusing on reducing costs while maintaining or improving product quality, businesses can deliver more value to customers, which strengthens their competitive position.
- Employee Engagement: Lean production often involves employees in the decision-making process, encouraging innovation and improving morale. A motivated workforce can lead to higher productivity and better customer service.
Summary
Stock control is a critical aspect of resource management in any business. By effectively managing stock levels, businesses can reduce costs, improve cash flow, and ensure that they can meet customer demand without unnecessary waste. Key elements such as buffer stock, just in time (JIT) management, and lean production can all contribute to more efficient operations. However, poor stock control can lead to stockouts, excess stock, and higher costs. Techniques like waste minimisation and the use of lean production strategies can help businesses gain a competitive advantage by improving efficiency, reducing waste, and providing high-quality products at lower costs.